Nederlands
Introductie
Voor 4-takt verbrandingsmotortjes is een overbrengverhouding van 1 op 2 nodig tussen de krukas en het kleppen systeem. Ik maak daarbij meestal gebruik van getande kunststof riempjes. Het kan ook met in elkaar grijpende tandwielen maar tandriemen hebben belangrijke voordelen:
1. De konstruktie vrijheid is groter omdat de hartafstand tussen de krukas en het klepsysteem dan niet bepaald wordt door de afmetingen van de tandwielen;
2. Er kan een grotere afstand overbrugd worden met relatief kleine getande wielen en de ruimte van de tandriem kan eenvoudig worden gecompenseerd met een spanwiel;
3. Een tandriem is geruisloos en hoeft niet gesmeerd te worden.
4. Het zelf maken van in elkaar grijpende tandwielen is een stuk moeilijker dan tandwielen voor getande riemen en men moet daamvoor ook over speciale moduulfrezen beschikken. Dit is niet of veel minder het geval met tandwielen voor tandriemen en daar gaat dit verhaaltje over.
Tandriemen
Er zijn tandriemen te koop in allerlei soorten en maten en ze zijn relatief goedkoop. Ikzelf gebruik altijd “Synchroflex” poly-urethaan tandriemen van het type T2,5 (2,5mm steek van de tanden) die versterkt zijn met dunne staaldraad en die 6 of 10mm breed zijn. Ze zijn erg soepel en ook erg sterk. Een goed adres voor deze riempjes is de fa Koppe in Wassenaar:
Technisch bureau Koppe B.V.
Verlengde Hoge Klei 24
2242 NS Wassenaar
Tel: 070-5119322
http://www.koppeaandrijftechniek.nl/contact/
Zij vertegenwoordigen o.a. de Fa Madler (Duitsland) waarvan ze de tandriempjes betrekt:
http://www.maedler.nl/
In de catalogus van Madler vindt je o.a. dit gegevensblad over 6mm brede tandriemen:
http://smarthost.maedler.de/datenblaetter/K39_153.pdf
Ze leveren blijkbaar ook bijbehorende tandwielen, maar ik die zijn behoorlijk duur. Bovendien moet je die ook altijd nawerken voor wat betreft het asgat en overige breedte maten. Dat is de reden waarom ik zelf een methode ontwikkeld heb om dit soort tandwielen eenvoudig zelf te maken van messing of een goede kwaliteit aluminium.
Het zelf maken van de getande wielen.
Ik draai eerst het gehele gladde wiel ook met het asgat en de tapgaatjes voor de bevestiging op de as. Het is van crusiaal belang dat de diameter van het gedeelte waar de tanden in gefreesd moeten worden tot op een tiende van een millimeter nauwkeurig gemaakt is om er voor te zorgen dat het riempje er mooi passend over heen zal lopen. Deze diameter wordt bepaald door het aantal tanden dat het wiel moet hebben. Op blad 2 van het tekeningpakket heb ik een lijst opgenomen van een aantal van deze wielen met verschillend aantal tanden en de daarbij behorende diameter.
De twee tandwielen die ik het meest gebruik hebben 36 respectievelijk 72 tanden, dus met een verhouding van 1 op 2. De diameters over de tanden zijn respectievelijk 28,10 en 56,80mm. De hoekopzet tussen de tanden is respectievelijk 10 en 5 graden omdat 36x10 en 72 x5 gelijk is aan 360 graden. Men moet dus wel beschikken over een draaitafel op de freesmachine om de hoekopzet nauwkeurig te kunnen maken. Mijn draaitafel heeft zelfs een voorziening om de juiste hoekverdraaiing te maken voor een willekeurig aantal tanden, zie Fig 1:
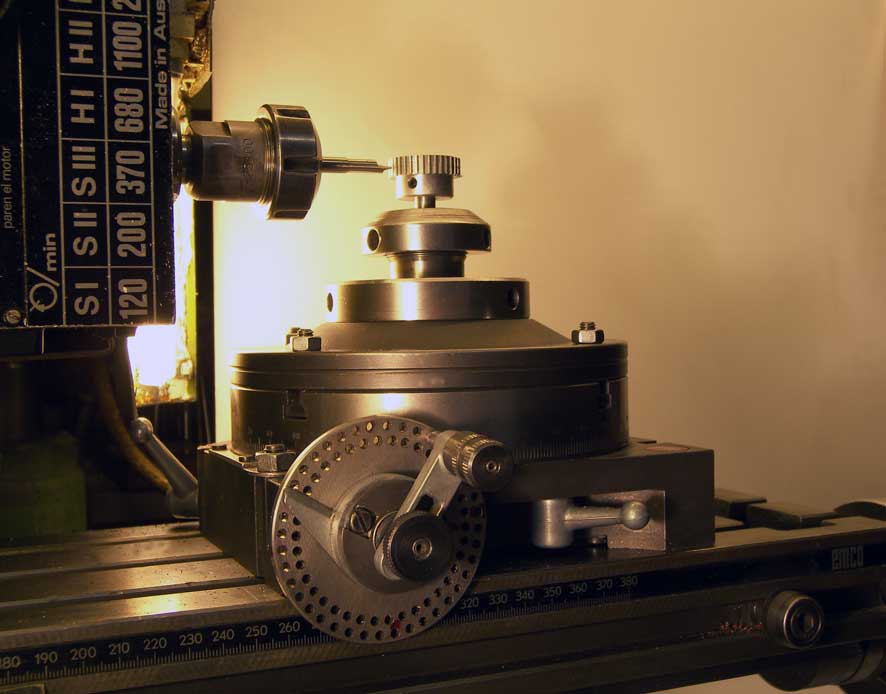
Fig.1
De eenvoudige frees is gemaakt van een HHS ponsnippel met 5mm diameter. Het snijgedeelte is eerst onder een hoek van 40 graden geslepen en daarna half weggeslepen zodat er twee snijkanten ontstaan, zie de figuren 2 en 3:
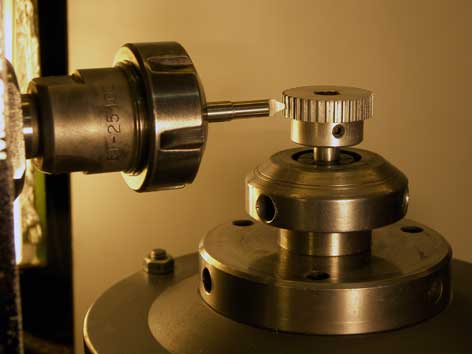
Fig 2
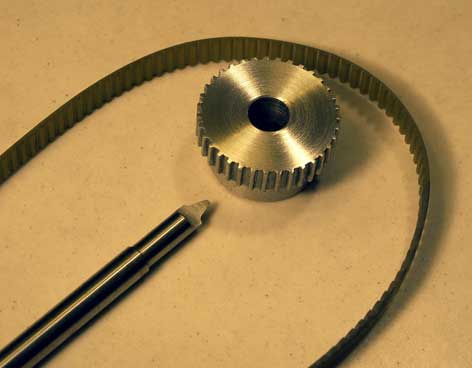
Fig 3
De freesdiepte is 0,9mm die met 2 of 3 opzetten gemaakt moet worden om mooi gladde vertandingen te krijgen. Het verdient aanbeveling om de tanden aan de bovenkant ietwat af te ronden bv. met een geschikt fijn sleutelvijltje en dan alles met een messing borstel of fijn schuurpapier na te werken. Als dit alles goed gedaan wordt zal het tandriempje mooi aansluiten en doet het tandwiel niet onder voor een gekocht en origineel tandwiel.
Tekeningpakket
Ik heb een 2- bladig tekenpakket gemaakt met daarop de nodige maten en gegevens; klik hier voor een aanvraag daarvoor.
English
Introduction
For 4-stroke engine distribution of 1 to 2 is needed between the crankshaft and the valve system. I usually use plastic (polyurethane) geared belt for that. It can also be done with interlocking gears but timing belts offer significant advantages:
1. Much more construction freedom because the center distance between the crankshaft and the valve system is not is determined by the dimensions of the gears;
2. A greater distance be covered with relatively small cog wheels and the geared belt can easily be stretched by a tensioning wheel;
3. A geared belt is silent and does not need to be lubricated.
4. Making your own interlocking gears is a lot harder than cog wheels for geared belts because one also must have the disposal of a special and (expensive) module cutter set. This is not the case with cog wheels for geared belts and that's what the story here is about.
Geared belts
There are timing belts for sale in all shapes and sizes and they are relatively cheap. Personally, I always use 6 or 10mm wide"SYNCHROFLEX" polyurethane timing belts type T2, 5 (2.5 mm pitch of the teeth) reinforced with thin steel wire; they are very flexible and strong.
There are numerous suppliers for all kinds of tooth belts on internet; type for instance “synchroflex timing belt” on Goggle Search. Here two examples:
http://www.beltingonline.com/polyurethane-timing-belts-182/synchroflex-4/synchroflex-t-series-73/?zenid=oc1nottoiqjn6l1rgo6r57qb95
and
http://www.transdev.co.uk/pages/belts/synchroflex/t2_5_main.htm
They mostly provide also associated cog wheels, but they are quite expensive in my opinion. Moreover one must finish them with respect to the shaft hole and all other dimensions. That is why I developed a method for making this type of gears easily yourself from a good quality of brass or aluminum.
The self-making of the cog wheels.
I first turn the entire wheel with bore for the shaft and tapped holes for fixing it on the the shaft. It is crusial that the diameter of the part where the teeth must be milled is accurate to a tenth of a millimeter to make sure that the geared belt will nicely fit over it. This diameter is determined by the number of teeth that the wheel should have. On page 2 of the drawing plan I have put a list of some of these wheels with different number of teeth and the corresponding diameters.
The two gears that I mostly use have 36 and 72 teeth, so with a ratio of 1 to 2. The diameters of the teeth are respectively 28.10 and 56.80 mm. The angle set-up between the teeth is 10 and 5 degrees respectively because 36x10 and 72x5 is equal to 360 degrees. One must therefore be equipped with a turntable on the mill with what the angle set-up can be made accurately. On my turntable there is even a provision for the proper angle set-up for an arbitrary number of teeth, see figure 1 above.The milling cutter is made of a HHS piercing punch nipple with 5mm diameter. The first cutting portion is grind at an angle of 40 degrees and thereafter ground half way so that there are two cutting edges, see figures 2 and 3 above.
The milling depth is 0.9 mm that must be made with 2 or 3 settings in order to get nice smooth cuts. It is recommended that the teeth on the top are somewhat rounded for example with a suitable fine key-file and then be finished with a brass brush or fine sandpaper. If all this is done well, the geared belt fit will fit nicely and this cog wheel will hardly or not differ from a purchased and original cog wheel.
Drawing plan
I made a 2-sheet plan on what you will find all dimensions and other data; click here for a request by e-mail.